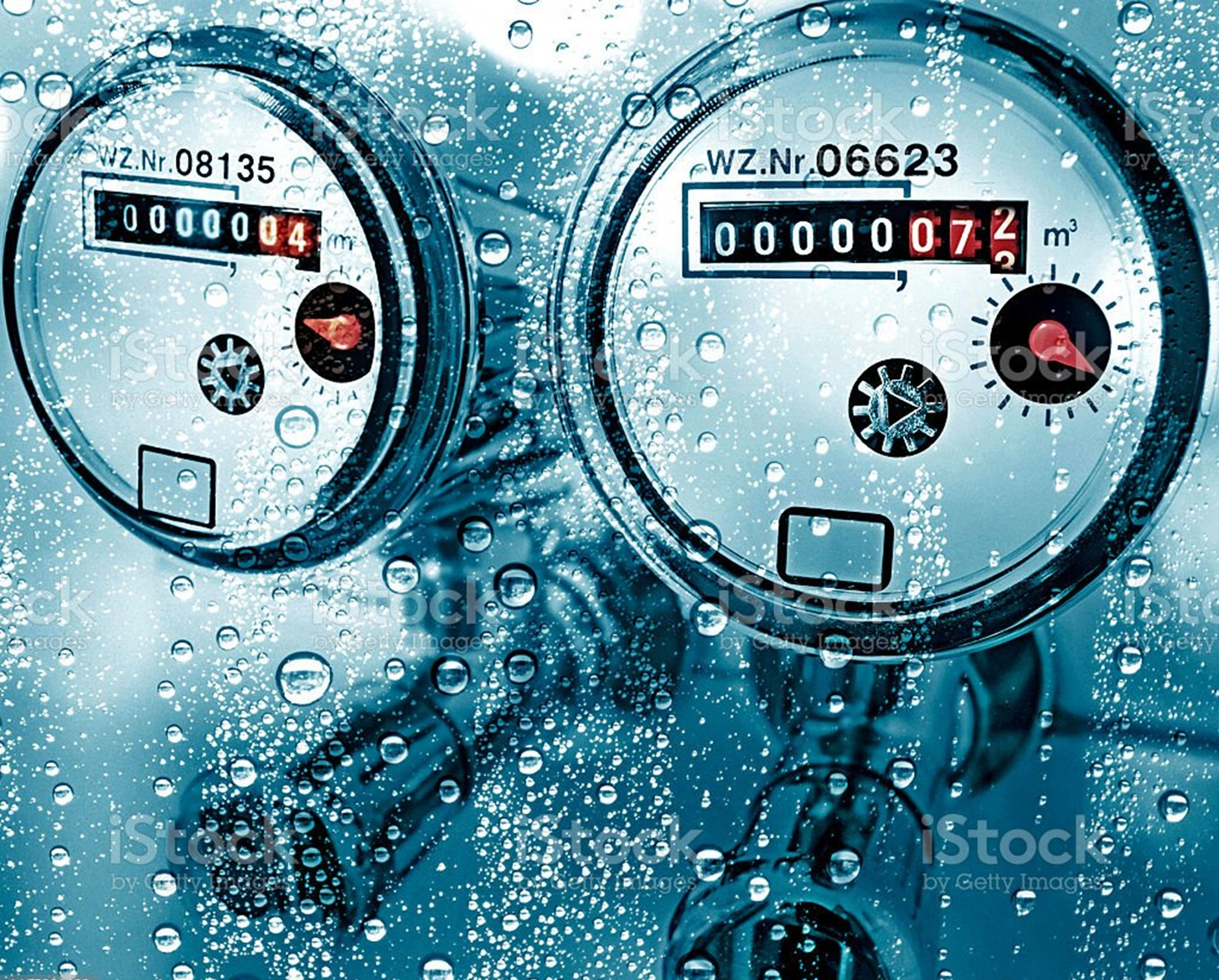
An Introduction To Flowmeters: Everything You Need To Know
1. INTRODUCTION
A flowmeter is an instrument that measures a liquid or gas’s linear, nonlinear, or angular speed. There are numerous varieties of flowmeters, each with a unique set of benefits and drawbacks. The most common types of flowmeters are electromagnetic, turbine, ultrasonic, positive displacement, differential pressure, Coriolis, and vortex.
Turbine flowmeters are the most popular flowmeter type due to their low cost, durability, and accuracy. Positive displacement flowmeters are a popular yet expensive option. Differential pressure flowmeters are the most accurate type of flowmeter but are difficult to install and maintain. Coriolis flowmeters are the most precise type of flowmeter and the most expensive. Vortex flowmeters are the least expensive type of flowmeter and the least accurate.
No matter what type of flowmeter you choose, selecting one that is appropriate for the application is important. Various factors such as fluid properties, operating conditions, and desired accuracy must be considered.
2. WHAT IS A FLOWMETER?
A flowmeter is a tool that gauges the rate at which a liquid or gas is moving. Flowmeters work by measuring the speed at which a substance flows through a pipe. They can be used to gauge how quickly fluids like air, water, steam, fuels, and chemicals are moving through a system.
Flowmeters come in a variety of shapes and sizes and can be used for a variety of applications including industrial process control, metering, and monitoring. The oil and gas, food and beverage, water treatment, and pharmaceutical industries are just a few that depend on them. Flowmeters are also used for medical purposes, such as monitoring blood flow, and for water and wastewater management.
Flowmeters measure flow rate in a variety of ways, such as through the displacement of a known volume of fluid, by measuring pressure drop, or through force balance.
Real-life examples of how flowmeters have been successfully used in a specific industry include measuring the flow rate of water in cooling towers, monitoring the flow of natural gas in pipelines, and controlling the flow of steam in power plants. In each case, flowmeters have helped to improve productivity, safety, and efficiency, by providing accurate and reliable measurement of flow rates and detecting any anomalies or leaks in the system.
3. WHY ARE FLOWMETERS IMPORTANT IN INDUSTRY?
Flowmeters provide accurate, real-time data on the flow rate of a process which can then be used to make decisions or adjust operations. This data can be used to improve efficiency, reduce waste, and increase productivity.
-
They increase efficiency by helping to prevent process upsets before they occur and by alerting operators to deviations from normal operations.
-
They also enable companies to monitor and control gas and liquid resources to reduce their environmental impact. By accurately measuring and controlling flows, businesses can reduce their energy consumption, eliminate waste, and optimize the use of resources. This assists companies in reducing operational expenses and ensuring environmental compliance.
Flowmeters are a critical component in any industrial process and are essential for accurate measurement and control of process flows.
(Image source: https://unsplash.com/@da_sikka_x)
4. DIFFERENT TYPES OF FLOWMETERS
Flowmeters come in many different shapes, sizes, and technologies. Flowmeters come in a variety of designs, including mechanical, electrical, and ultrasonic. A few common types of flowmeters include:
-
Mechanical flowmeters – These use physical mechanisms such as a paddle, turbine, or rotating vane, to measure the flow rate of the fluid. As the fluid flows through the device, it interacts with the mechanism, causing it to rotate. The rate of rotation is proportional to the flow rate of the fluid, which can be measured and displayed on a gauge or other readout.
-
Turbine Flowmeters – These measure the flow rate of liquid or gas by using an array of paddles that rotate when the liquid or gas passes between them. The rate of flow is directly proportional to the rotational speed of the paddles.
-
Electrical flowmeters – These use sensors and electronics to measure the flow rate. These devices may use electromagnetic, thermal, or ultrasonic sensors to detect the flow of the fluid and convert it into an electrical signal. This signal can then be processed and displayed as a digital readout.
-
Ultrasonic Flowmeters – These measure the flow rate of liquid or gas using high-frequency sound waves emitted by a transducer. The transducer sends an ultrasonic signal that is reflected by the walls of the pipe and received by a receiving transducer. The pace of flow is related to the amount of time between the waves’ transmission and reception.
-
Vortex Flowmeters – These measure the flow rate of liquid or gas by using the principles of Bernoulli’s principles. Alternating vortices that are directly proportional to the fluid’s velocity are produced by a vortex generator.
-
Mass Flowmeters – These measure the flow rate of liquid or gas by weighing the amount of material that passes through the meter. Applications where accuracy is crucial employ this kind of meter. Examples include Coriolis flowmeters and thermal flowmeters.
-
Magnetic/Electromagnetic Flowmeters – These measure the flow rate of liquid or gas by measuring the magnetic pulses generated by an electrical current passing through the liquid or gas. The pulses are then used to calculate the rate of flow.
-
Differential Pressure Flowmeters – These function by determining the variation in pressure across two pipeline sites. The orifice plate, which comprises a thin plate with a hole in the center, is the most popular type of differential pressure flowmeter. Other types include venturi meters, flow nozzles, and pitot tubes.
-
Positive Displacement Flowmeters – These flowmeters function by counting the amount of fluid that flows through the pipeline. Rotating and reciprocating are the two subtypes that can be further broken down. Examples include nutating disk meters, oval gear meters, and piston meters.
-
Velocity Flowmeters – These function by gauging the fluid’s flow rate through the pipeline. Examples of velocity flowmeters include electromagnetic flowmeters, ultrasonic flowmeters, and turbine flowmeters.
-
Open Channel Flowmeters – These gauge the pace at which liquids move along unobstructed channels like rivers, canals, and streams. Weirs, flumes, and current meters are a few examples.
5. HOW DO YOU CHOOSE THE BEST FLOWMETER FOR YOUR APPLICATION?
Selecting the right flowmeter for a specific application mostly depends upon the characteristics of the fluid that needs to be measured. Flowmeters vary in terms of their accuracy, repeatability, temperature, pressure, and other ranges, and this can all make a difference in determining the best flowmeter for an application.
In addition, based on an analysis of the application’s hydraulic parameters, flow regime, and type of fluid, the selection of the best flowmeter can also vary. For example, a magnetic flowmeter is better suited for conducting liquids like water, acids, and other conductive liquids, while a turbine flowmeter is best for measuring non-conductive liquids like petrol and diesel. The choice of the best flowmeter for the application is also dependent upon the nature of the application, the cost range, and other requirements.
Ultimately, each flowmeter selection should be based on its application-specific requirements like accuracy and repeatability, as well as cost and installability. It is always recommended to consult a trained application engineer to ensure that the most suitable flowmeter is selected.
(Image source: https://pixabay.com/illustrations/pipeline-gate-valve-flow-meter-1585686/)
6. INSTALLATION AND MAINTENANCE
Once you have selected the best flowmeter for your application, proper installation and maintenance become important for long-term efficient operation. Poor installation or failure to maintain the flowmeter can result in inaccurate readings or could even lead to significant unexpected costs from breakdowns or other faults.
-
Flowmeter installation usually involves mounting the flowmeter onto the pipe, running any sensors, or wiring connections, and then configuring and calibrating them.
-
It should be installed in such a way that it is not affected by any vibrations or temperature fluctuations and offers frequent access for maintenance.
-
To keep the flowmeter running optimally, regular maintenance and testing are recommended.
-
Daily checks should be done to ensure that the instrument is working properly and that there are no signs of wear and tear.
-
Also, regular calibrations should be undertaken to compare the flowmeter’s readings with the expected values.
-
Additionally, the flowmeter should be regularly cleaned, serviced, and inspected to ensure proper operation and accuracy.
7. TROUBLESHOOTING
It may be that after proper installation and maintenance, you are still encountering further issues with your flowmeter. In such cases, common troubleshooting practices should be used to diagnose and repair whatever problem you are experiencing.
-
First and foremost, you should check if all the wiring and connections are okay, and that nothing is loose or disconnected.
-
Also ensure that all the seals, rings, and other components are in good shape and that nothing is blocking the flowmeter.
-
If the scan gauge indicates the readings are unreliable or inaccurate, you should first test the flowmeter using a different medium or fuel to check if the problem persists or not.
-
Also check the other components in the device such as the temperature sender, pressure sender, amplifier, or any other part.
If all the components and connections are okay and the flowmeter is still not functioning properly, it could be that the flowmeter is damaged or defective. If this is the case, then the flowmeter needs to be replaced or repaired accordingly.
8. CONCLUSION
The flow meter is one of the most important tools for measuring volumetric flow rates with accuracy and precision. From oil and gas to wastewater treatment, and industrial processes, flowmeters are used in many various applications. Proper installation and maintenance are critical for the flowmeter to function accurately and with reliable readings.
The technology advances, numerous types of flowmeters, and the various materials they come in can make the selection process a bit overwhelming. Nonetheless, taking the time to research and understand each type and its applications can help you make the right decision for your project.
In addition to research and careful selection, proper maintenance and troubleshooting techniques should be carried out when issues arise. Understanding where and how to deploy the right flowmeter, safely and efficiently, is essential for getting accurate results. Hopefully, this article has given you the knowledge and guidance you need to select and install a flowmeter.